Turning of connector housing
- PRODUCT DETAIL
Turning is part of CNC machining. Lathe processing mainly uses a turning tool to turn a rotating workpiece. Lathes are mainly used for machining shafts, discs, sleeves and other rotating or non-rotating workpieces with rotating surfaces. It is the most widely used machine tool processing in the RF connector shell factory.
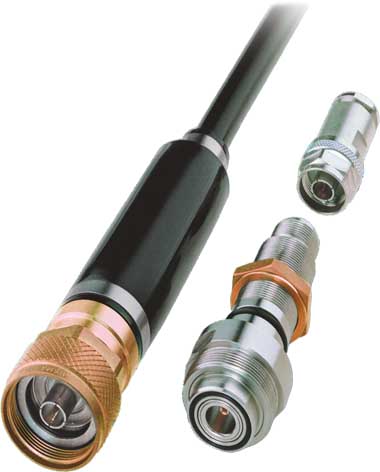
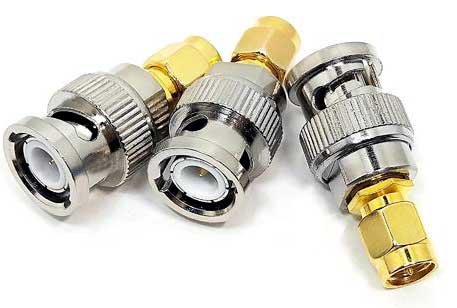
Turning technical issues
Turning is one of the most widely used in the machine manufacturing industry. The number of lathes is large, the staff is large, and the processing range is wide. There are many tools and fixtures used, so the safety technology of turning is particularly important. The key tasks are as follows:
1. Damage from cutting chips and protective measures. The toughness of various steel parts processed on the lathe is better, the chips produced during turning are full of plastic curl, and the edges are relatively sharp. During high-speed cutting of steel parts, red hot and long chips are formed, which are very easy to hurt people. At the same time, it is often wound on the workpiece, turning tool and tool holder, so the iron hook should be used to clean or break in time during work. Stop to remove when necessary, but never remove or pull off by hand. In order to prevent chip damage, chip breaking, chip flow control measures and various protective baffles are often taken. The chip breaking measure is to grind chip breakers or steps on the turning tool; Use appropriate chip breakers and mechanical clamping tools.
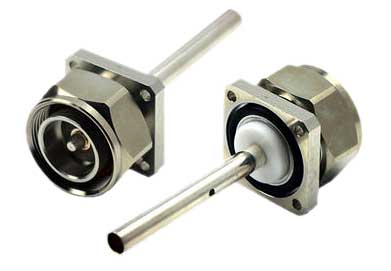
3. Safe operation.
Before working, check the machine tool thoroughly and confirm it is good before use. The clamping of the workpiece and the tool ensures the correct position, firmness and reliability. During processing, the machine must stop when changing tools, loading and unloading workpieces, and measuring workpieces. Do not touch the workpiece or wipe it with cotton silk when rotating. The cutting speed, feed rate and strenuous depth must be selected appropriately, and overload processing is not allowed. Workpieces, fixtures and other sundries shall not be placed on the head of the bed, the knife rest and the bed surface. When using a file, move the turning tool to a safe position, with the right hand in front and the left hand in the back to prevent the sleeves from being caught. The machine tool must have a dedicated person responsible for use and maintenance, and other personnel must not use it.
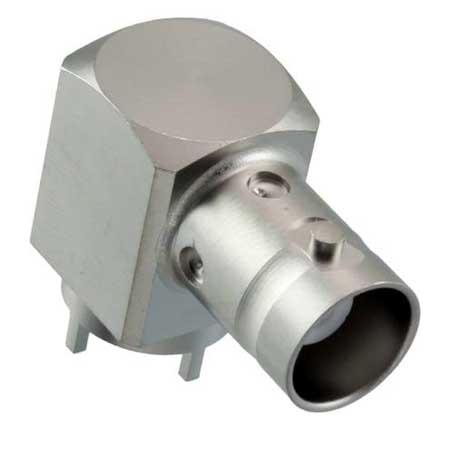
General sequence of turning processing
1) When turning a stepped shaft, in order to ensure the rigidity during turning, generally the part with the larger diameter should be turned first, and the part with the smaller diameter should be turned afterwards.
2) When grooving the workpiece on the shaft, it should be carried out before finishing to prevent deformation of the workpiece.
3) When finishing a threaded shaft, generally the unthreaded part should be finished after threading.
4) Before drilling, the end face of the workpiece should be flattened. If necessary, punch the center hole first.
5) When drilling deep holes, generally drill pilot holes first.
6) When turning (Φ10—Φ20) mm holes, the diameter of the tool holder should be 0.6—0.7 times the processed hole diameter; When machining holes with a diameter greater than Φ20mm, generally the tool holder with the tool head should be used.
7) When turning multiple threads or multiple worms, try cutting after adjusting the gears.
8) When using an automatic lathe, adjust the relative position of the tool and the workpiece according to the machine adjustment card. Test turning is required after adjustment, and the first piece can be processed only after it is qualified; Pay attention to tool wear and workpiece size and surface roughness at any time during processing.
9) When turning on a vertical lathe, after the tool post is adjusted, the beam cannot be moved at will.
10) When the relevant surface of the workpiece has position tolerance requirements, try to complete the turning in one clamping.
11) When turning the cylindrical gear blank, the hole and the reference end face must be processed in one clamping. If necessary, a marking line should be drawn near the gear index circle on the end face.
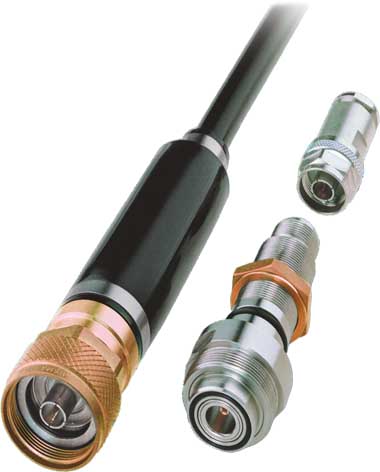
Introduction to Turning Technology
Turning processing is on the lathe. Use the rotary motion of the workpiece and the linear or curved motion of the tool to change the shape and size of the blank, and process it to meet the requirements of the drawing. Turning is a method of cutting the workpiece on the lathe by rotating the workpiece relative to the tool. Turning is the most basic and common cutting method. It occupies a very important position in production. Turning is suitable for machining revolving surfaces, and most workpieces with revolving surfaces can be processed by turning methods. Such as: inner and outer cylindrical surface, inner and outer conical surface, end surface, groove, thread and rotary forming surface. The tools used are mainly turning tools. The radio frequency coaxial connector is a typical cylindrical rotary forming product.
Among all kinds of metal cutting machine tools, lathes are the most widely used, accounting for about 50% of the total number of machine tools. The lathe can not only use turning tools to turn the workpiece, but also use drills, reamers, taps and knurling tools for drilling, reaming, tapping and knurling operations. According to different process characteristics, layout forms and structural characteristics, lathes can be divided into horizontal lathes, floor lathes, vertical lathes, turret lathes, and profiling lathes. Most of them are horizontal lathes.
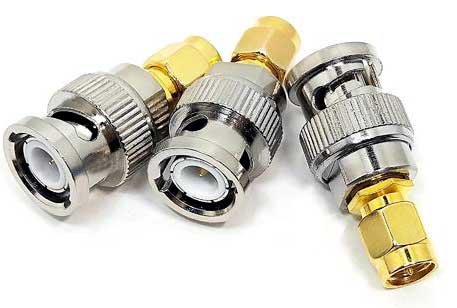
Turning technical issues
Turning is one of the most widely used in the machine manufacturing industry. The number of lathes is large, the staff is large, and the processing range is wide. There are many tools and fixtures used, so the safety technology of turning is particularly important. The key tasks are as follows:
1. Damage from cutting chips and protective measures. The toughness of various steel parts processed on the lathe is better, the chips produced during turning are full of plastic curl, and the edges are relatively sharp. During high-speed cutting of steel parts, red hot and long chips are formed, which are very easy to hurt people. At the same time, it is often wound on the workpiece, turning tool and tool holder, so the iron hook should be used to clean or break in time during work. Stop to remove when necessary, but never remove or pull off by hand. In order to prevent chip damage, chip breaking, chip flow control measures and various protective baffles are often taken. The chip breaking measure is to grind chip breakers or steps on the turning tool; Use appropriate chip breakers and mechanical clamping tools.
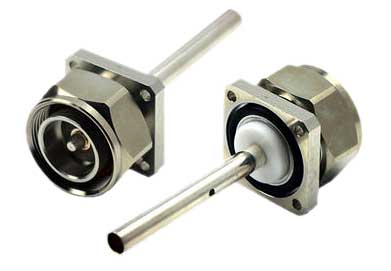
2. Clamping of the workpiece.
In the process of turning, there are many accidents that damage the machine tool, break or break the tool, and cause the workpiece to fall or fly out due to improper clamping of the workpiece. Therefore, in order to ensure the safe production of turning processing, special attention must be paid when loading the workpiece. Appropriate clamps should be selected for parts of different sizes and shapes, regardless of whether the three-jaw, four-jaw chuck or the connection between the special clamp and the spindle must be stable and reliable. The workpiece should be clamped and clamped. The sleeve can be used to clamp the large workpiece to ensure that the workpiece does not shift, fall off or throw out when the workpiece is rotated at high speed and cut. If necessary, use the center frame, center frame, etc. to enhance the clamping. Remove the handle immediately after the card is tightened.
In the process of turning, there are many accidents that damage the machine tool, break or break the tool, and cause the workpiece to fall or fly out due to improper clamping of the workpiece. Therefore, in order to ensure the safe production of turning processing, special attention must be paid when loading the workpiece. Appropriate clamps should be selected for parts of different sizes and shapes, regardless of whether the three-jaw, four-jaw chuck or the connection between the special clamp and the spindle must be stable and reliable. The workpiece should be clamped and clamped. The sleeve can be used to clamp the large workpiece to ensure that the workpiece does not shift, fall off or throw out when the workpiece is rotated at high speed and cut. If necessary, use the center frame, center frame, etc. to enhance the clamping. Remove the handle immediately after the card is tightened.
3. Safe operation.
Before working, check the machine tool thoroughly and confirm it is good before use. The clamping of the workpiece and the tool ensures the correct position, firmness and reliability. During processing, the machine must stop when changing tools, loading and unloading workpieces, and measuring workpieces. Do not touch the workpiece or wipe it with cotton silk when rotating. The cutting speed, feed rate and strenuous depth must be selected appropriately, and overload processing is not allowed. Workpieces, fixtures and other sundries shall not be placed on the head of the bed, the knife rest and the bed surface. When using a file, move the turning tool to a safe position, with the right hand in front and the left hand in the back to prevent the sleeves from being caught. The machine tool must have a dedicated person responsible for use and maintenance, and other personnel must not use it.
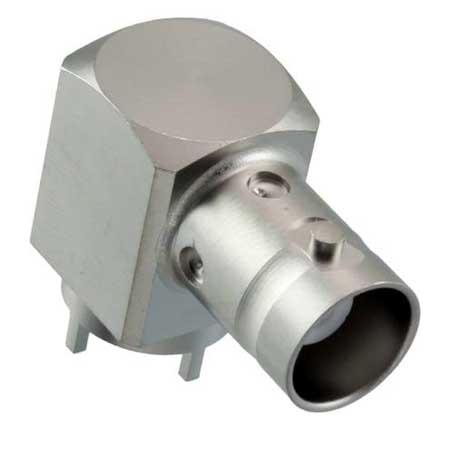
General sequence of turning processing
1) When turning a stepped shaft, in order to ensure the rigidity during turning, generally the part with the larger diameter should be turned first, and the part with the smaller diameter should be turned afterwards.
2) When grooving the workpiece on the shaft, it should be carried out before finishing to prevent deformation of the workpiece.
3) When finishing a threaded shaft, generally the unthreaded part should be finished after threading.
4) Before drilling, the end face of the workpiece should be flattened. If necessary, punch the center hole first.
5) When drilling deep holes, generally drill pilot holes first.
6) When turning (Φ10—Φ20) mm holes, the diameter of the tool holder should be 0.6—0.7 times the processed hole diameter; When machining holes with a diameter greater than Φ20mm, generally the tool holder with the tool head should be used.
7) When turning multiple threads or multiple worms, try cutting after adjusting the gears.
8) When using an automatic lathe, adjust the relative position of the tool and the workpiece according to the machine adjustment card. Test turning is required after adjustment, and the first piece can be processed only after it is qualified; Pay attention to tool wear and workpiece size and surface roughness at any time during processing.
9) When turning on a vertical lathe, after the tool post is adjusted, the beam cannot be moved at will.
10) When the relevant surface of the workpiece has position tolerance requirements, try to complete the turning in one clamping.
11) When turning the cylindrical gear blank, the hole and the reference end face must be processed in one clamping. If necessary, a marking line should be drawn near the gear index circle on the end face.